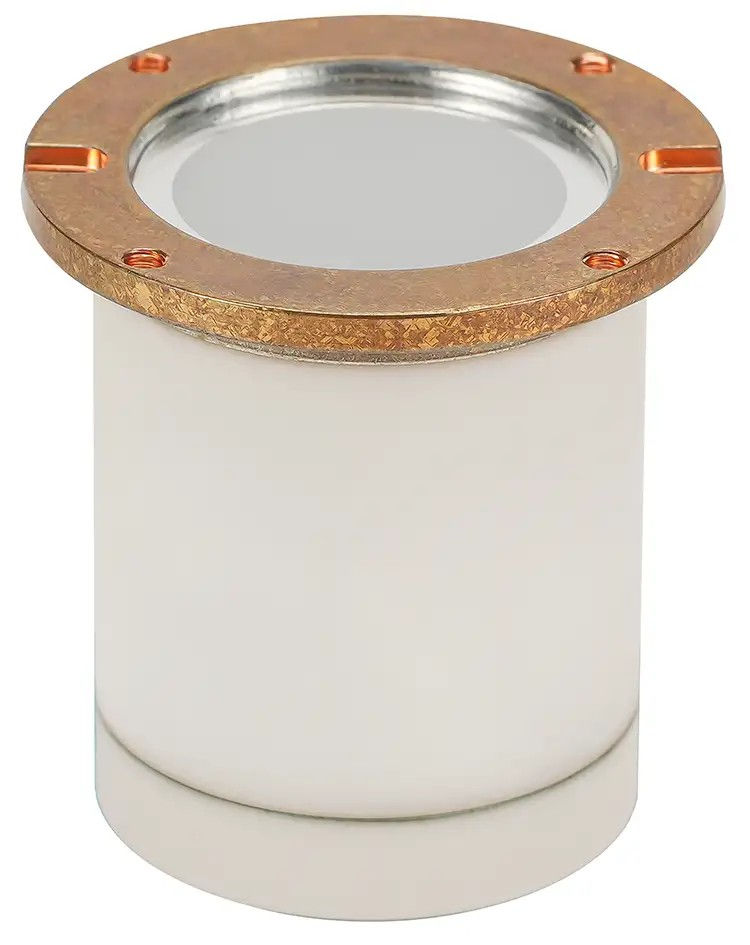
Elec-field Future Corporation is a Gyeonggi-do, South Korea, manufacturer of carbon nanotube (CNT) X-ray and UV lamps, as well as a manufacturer of modular UV disinfection equipment systems and digital X-ray equipment systems that feature the company’s CNT lamps. Elec-field Future is a 2024 IUVA RadLaunch awardee, honored for its CNT UV disinfection lamp which incorporates nanotechnology to produce 300 W output of 273 nm UV-C energy. The CNT UV lamp and UV disinfection system are intended for water purification, residential disinfection applications, bio cleanroom use and implementation in vertical farming.
The lamp includes directional design to focus the emitted UV light, and its digital design allows for the generation of non-colored UV emissions. The use of CNT materials eliminates the environmental concerns of traditional mercury-based UV lamps and gives the lamp a product lifespan of three years. The CNT UV lamp measures 38 pi x 35.1 mm, in an overall disinfection system of 300 x 205 x 217 mm. Following completion of the product prototype, in-the-field verification now is being conducted at a water treatment facility.

Elec-field Future manufactures its CNT UV lamps with high-vacuum brazing to produce a sealed light source. The manufacturing process includes optimization of the anode window material, thickness, surface enhancement control and aluminum metal reflection film coating for superior UV-C sterilization light transmittance. The anode has a 1 mm-thick sapphire substrate, a 20 µm-thick UV-C phosphor layer (YLaPO4:Pr) and a 100 nm-thick aluminum (Al) electrode. The electron beam is focused by the acceleration voltage applied to the anode electrode and the lamp’s focusing electrode structure.
The heart of the company’s innovation is its use of nanotechnology, incorporating the company’s own arc-discharge CNT synthesis to deliver high-performance advanced carbon nanomaterial. Although the first carbon nanotube was synthesized 30-some years ago, researchers and materials engineers still are discovering new properties and novel applications for CNTs.
A carbon nanotube is formed at the nanoscale from a sheet of carbon atoms, with the sheet rolled into a seamless hollow cylinder. The configuration in which a sheet is rolled – its chirality – modifies the properties exhibited by the nanotube. CNT material is more flexible than rubber, has higher tensile strength than steel and has thermal conductivity. CNTs can be semiconductors or provide electrical conductivity. They can sense, absorb and emit light in a wide spectral range and can be fine-tuned to a particular wavelength. They are being used in everything from body armor to visual displays to tennis rackets to yachts, and researchers and scientists have only scratched the surface of their potential use as the newest building block in the toolbox.
CEO Hansung Lee offered some insight into the company’s carbon nanotechnology. “We are producing single-walled nanotubes and multi-walled nanotubes,” Lee explained. “Our UV lamp uses thin, multi-walled carbon nanotubes as an electron emission source.” The company chose arc-discharge synthesis as its carbon nanotube production method.
“CNTs synthesized by arc-discharge,” said Lee, “possess high crystallinity and excellent thermal stability because they are produced at high temperature (~5000℃). The principle of this technique is to vaporize carbon in the reduced atmosphere of inert gas. After the triggering of the arc between two electrodes, plasma is formed consisting of the mixture of carbon vapor, the rare gas. Vaporization is the consequence of the energy transfer from the arc to the graphite-doped anode. The anode erosion rate is more or less important depending on the power of the arc and also dependent on the other experimental conditions. Carbon nanotubes then self-assemble from the vapor.”
In the past, the use of arc-discharge synthesis to manufacture CNTs has had drawbacks in production speed and production capacity. Elec-field Future has overcome those limitations.
“The conventional multi-walled carbon nanotube synthesis method using the arc-discharge method has the disadvantage that the growth rate is very slow, and the synthesis process is completed quickly – within 10 minutes,” Lee explained. “The arc-discharge method that we have devised has a very fast carbon nanotube growth rate and can be synthesized for more than 30 minutes. Our method also delivers material with very high purity.”
He continued, “We also are working to develop products with a wavelength of 222 nm that are harmless to the human body. Therefore, when the development of phosphor with a wavelength of 222 nm is completed, it seems that the B2B, B2C market also will achieve great results.”